IIT Bombay researchers use new technique to measure rate of degradation of coatings on iron
Combining two electrochemical techniques, hydrogen permeation-based potentiometry (HPP) and electrochemical impedance spectroscopy (EIS), the researchers efficiently measured the coating degradation rates on the industrially relevant metal.
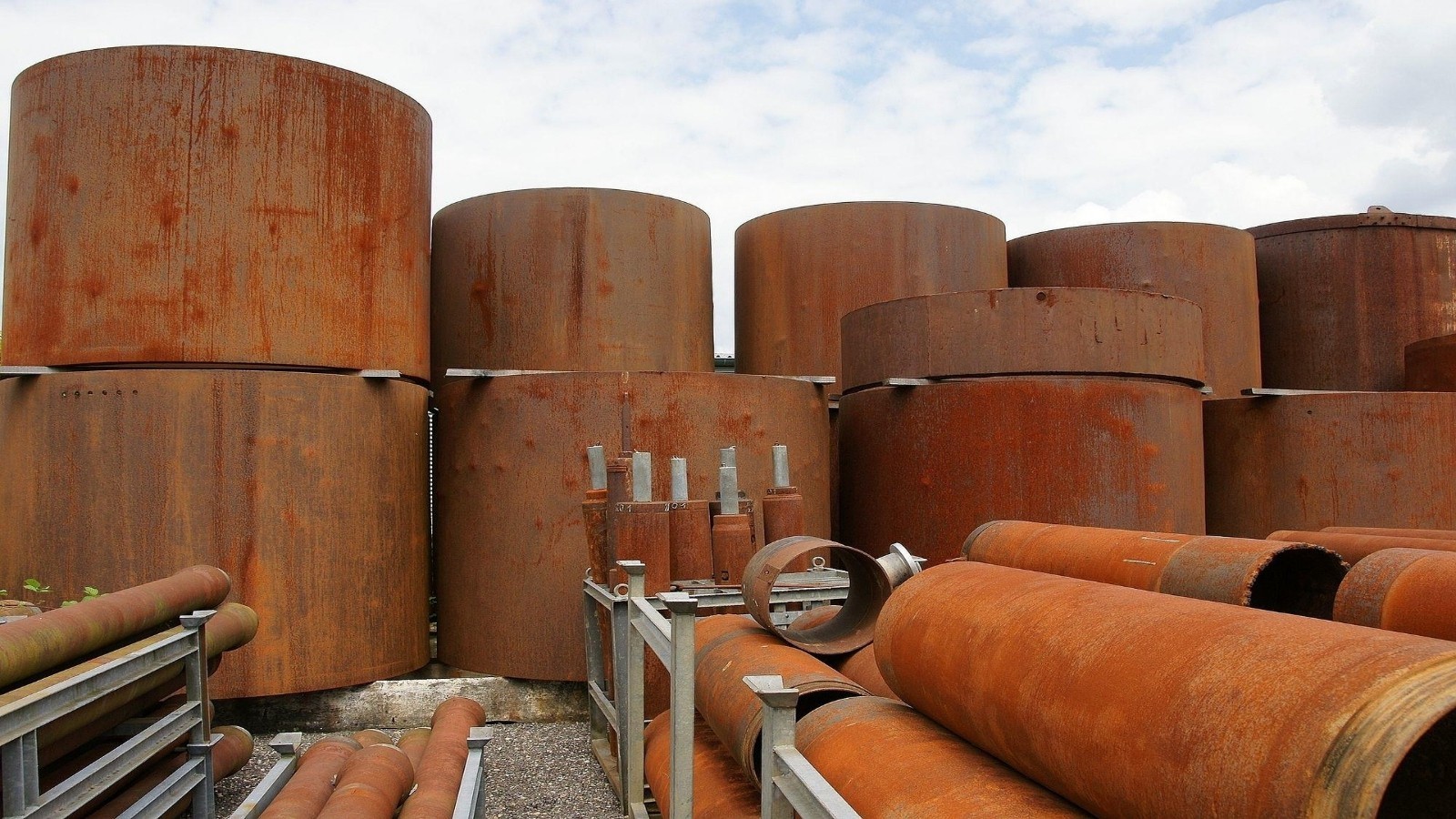
Metals corrode with time, and some metals corrode more than others, e.g., iron rusts in days, while gold and silver take decades or centuries to deteriorate. Metals often have a layer of protective coating, like the paint on our cars, to prevent corrosion. A more efficient way of protecting metals is by coating them with organic coatings. Organic coatings are layers of carbon-based polymeric substances, natural or synthetic, applied in the form of paints and varnishes. According to a recent market analysis report by Grand View Research, the market for such corrosion inhibitors is a USD 8.93 billion market projected to grow at 3.6% annually from 2025 to 2030.
The efficiency of organic coatings deteriorates with time, eventually damaging the metal. That is because the coatings have pores and defects that allow water and oxygen to reach the underlying metal surface over time and corrode it. The coating wears with time because of a fundamental electrochemical process called oxygen reduction reaction (ORR), where molecular oxygen gets reduced to water, hydrogen peroxide or hydroxyl ions. This process occurs in various electrochemical devices, including fuel cells and metal-air batteries. Understanding the rate at which ORR occurs is important to know how quickly the coating may give way for the metal to corrode. This knowledge is critical in several industrial applications.
Traditional techniques, such as linear sweep voltammetry and potentiodynamic polarization, used to measure ORR rate are based on electrochemistry, i.e., chemical reactions that produce or consume electrical energy. In linear sweep voltammetry, a continuously changing voltage is applied to the metal and the current generated in response to it is measured. The resulting current-voltage curve provides insights into the rate at which ORR can occur on the metal. However, in coated metals, because organic coatings block the passage of ions required to generate current, the rate at which the coating degrades is often representative of current generated only at pre-existing tiny holes in the coating. This may not reflect the actual degradation rate at the interface.
A couple of years ago, researchers led by Prof Vijayshankar Dandapani at the Department of Metallurgical Engineering and Materials Science at the Indian Institute of Technology Bombay (IIT Bombay) established an improved quantitative method to characterise the performance of organic coatings used for corrosion protection.
In their innovative approach, the IIT Bombay researchers combined hydrogen permeation-based potentiometry (HPP) with electrochemical impedance spectroscopy (EIS). In the HPP setup, researchers apply an electrical current on one side of the metal to generate hydrogen. The hydrogen atoms then permeate through the metal and cause changes in electrochemical potential measured on the other side containing oxygen. In this way, the amount of hydrogen that has passed through the metal is used as a sensor to measure the ORR rate.
EIS is a technique used to analyse how materials respond to electrical signals. An alternating current (AC) voltage is applied to the material, and the resulting current response is measured, from which the material’s impedance (or resistance) can be calculated. The impedance value associated with different processes occurring on the metal surface, including hydrogen-induced ORR progress, can be monitored at a certain frequency of the AC signal.
Combining HPP and EIS techniques allowed the researchers to quantify the degradation rates at the interface between the organic coating and the metal. While HPP gives a direct measure of hydrogen permeation, EIS provides insights into how hydrogen permeation corrodes the coated metal.
“The idea itself came from an attempt to find if a complementary technique such as EIS can be used to strengthen the interpretations from the hydrogen permeation-based potentiometry (HPP) approach,” says Prof Vijayshankar.
In their earlier study, the researchers provided a proof-of-concept by measuring ORR at the interface between a model polymer coating and palladium metal using HPP and EIS. In this new study, the IIT Bombay group, along with researchers from the University in Brest, France, have extended this application to an important industrial metal, namely, iron.
This study received funding from the Indo-French Centre for Promotion of Advanced Research -CEFIPRA and the Science and Engineering Research Board (SERB), India.
The researchers coated a thin layer of iron on palladium membranes and coated the iron with a polymer called poly-methyl methacrylate (PMMA). They measured the rate at which oxygen reduction reaction occurred at the interface between PMMA and iron using HPP-EIS. They captured the current-potential (I(U)) curves and corresponding impedance values, which they found to be higher than that for a bare iron surface. High impedance values correspond to low corrosion rates and vice versa. This validated the use of the HPP-EIS technique to evaluate ORR occurring at interfaces that one cannot easily study using the traditional methods because the interface between organic coatings and metals is buried and inaccessible.
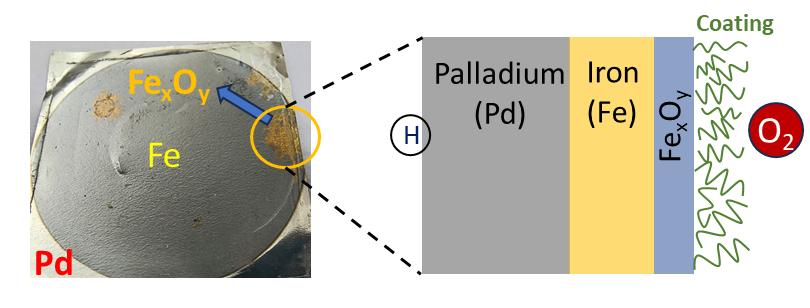
HPP-EIS is cost-effective because it requires only two potentiostats, simple electronic devices that control and measure the voltage between two electrodes.
So, HPP-EIS can be used to monitor how quickly the organic coating will give way for the iron to rust in this particular instance. According to Prof Vijayshankar, this method would be of interest not only to the steel industry but will also be useful in the field of fuel cells and sensors.
With hydrogen blending becoming increasingly popular to reduce emissions from natural gas, one can also apply HPP-EIS technique “to determine how quickly the coat of paint on a natural gas pipeline where hydrogen is blended with natural gas degrades,” says Prof Vijayshankar, highlighting a potential application.
Article written by | Joel P Joseph |
Image/Graphics credit | Image by peter731 from Pixabay |
link to gubbi labs | - |
